How do you convey to your manufacturers and designers the features that are most important to the success of your wire harness? If you’re not working with a manufacturer that has years of experience in a variety of fields, it can be tough to ensure that they have a full grasp of the wide array of conditions that your product needs to be able to function and work efficiently while including the right components for your wire harness. To help you do this, it’s important to assess which conditions and factors must be taken into consideration when crafting wire harnesses.
How does the location of the wire harness factor into its development?
An important first step is to consider the location that your Wire Harness will likely be in:
- Will this product be indoors or outdoors?
- Will the wires and cables used be exposed or housed within a product?
- What kind of temperatures do you expect the product to be in? Is it likely to be extremely hot or cold?
- Will the wiring be pulled on or bent? Will a coil cord be useful so that the product can stretch and retract neatly?
- Are chemicals, water, or other wires expected to be near this product?
This is a useful set of questions to begin considering when conveying your product’s needs and specifications to a design team. There are extensive lists of industry standards and guidelines to follow when determining the best type of wiring to utilize and these are just a few of the factors to consider in this process. For this reason, as well as safety concerns, it’s important that you work with a manufacturer who is familiar with both national and international standards depending on the scope of your product’s market.
How do outdoor and indoor Wire Harnesses vary?
If your product is intended for outdoor use, you’ll likely be in the market for a thicker set of cables. This will likely require the use of a cable assembly, as they are more durable and have several layers of insulation to stand up to wear-and-tear. This will also be more effective if you need to cover larger distances. These cables are typically insulated by heavy-duty materials, such as shrink-wrapped thermoplastic, thermoplastic rubber, or vinyl.
If your product is intended for indoor use, a wire harness will likely be the best option, assuming the product will not be exposed to any harsh conditions or liquids. Wire harnesses are also ideal in situations that require a cost effective solution for transporting electricity or a signal over a shorter distance due to their smaller size and carrying capacity.
Another factor to consider is whether or not the harness will be housed in another product. If so, you’ll need to consider the functionality of the product it’s going into. Does this product have several moving parts that could alter its temperature, is there a chance that the product could leak or malfunction in a way that may cause the harness to get wet or be introduced to chemicals? Using a manufacturer that creates and tests prototypes during the production process will allow designers to foresee and prevent errors before production begins on a large scale.
Materials to combat temperature restrictions on Wire Harnesses
For cold conditions, coatings that will not become brittle or rigid as a result of the cool climate should be considered. These products should be able to expand and contract as they move in and out of frigid temperatures. Ask your manufacturer to see the product specifications and certifications laid out by bodies such as UL.
For extremely hot conditions, you’ll need to discuss with your manufacturer what types of temperatures the rest of the product could potentially reach and determine the heat tolerance that your wire harness will require to meet safety standards and specifications.
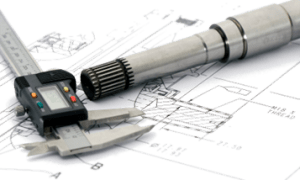
Quality Wire Harness Manufacturing
Elements to keep in mind when discussing materials suited to extreme temperatures include:
- Conductor Insulation
- Wraps
- Jacket
Type of Conductor
The conductor is what your signal or current will actually be transmitted through. The type of conductor used must be suitable to withstand certain conditions without overheating or corroding. Some things to consider when discussing conductors are:
- The voltage or bandwidth that the conductor needs to be able to carry without exceeding its carrying capacity and potentially overheating or becoming attenuated.
- The type of metal and coatings used. Copper is one of the most common conductors due to its high conductivity. But, copper is very prone to corrosion, making it important to determine what your wire will be exposed to and the appropriate coatings needed to combat this.
Other Elements to Consider when Choosing the Right Wire Harness Components
Aside from these basic elements, there are a variety of additional features that may add additional functionality to your wire harness including:
- Terminals: this is the point at which the wire ends, it may be connected to another component or capped off depending on its use and location.
- Connectors: there are a variety of connectors used to marry different wires together. Some of these are permanently affixed to the system, while others are removable for products that are likely to be portable or require interchangeable parts.
- Strain Relief: this is a system designed to throttle currents as they reach the terminal, this is intended to prolong the life of the terminal.
- Grommets: utilizing grommets will keep wires secure and in their proper place. Grommets help to maintain an organized system and will make installation and any maintenance on the product more efficient.
Choosing the right components for your product’s wire harness is vital to ensuring that you have a product that will meet your unique design standards and run efficiently. Entrusting your product with a manufacturer that has experience and an understanding of a variety of fields will make the process much easier. Additionally, it’s important that you choose a manufacturer who is willing to gain an understanding of your product’s individual needs and specifications.