At its most basic, cable assemblies starts with group of wires or cables covered by more intensive exterior product, twisted together in different gauges.All serve different purposes like transmitting power or a signal, adding different filler materials based on the application, and finally wrapping up the whole package in a protective outer jacket. In general, they are made from heavy-duty materials including shrink-wrapped thermoplastic, thermoplastic rubber, or vinyl. These workhorses provide the ability for everyday necessities like cell phone chargers and your television and sound system to connect but also range to the incredibly complex like a Formula One’s electrical system or the controls inside of a battle tank. Truth is, cable assemblies are used in just about every facet of everyday life. With precise design and solid manufacturing, today’s custom cable assemblies can withstand just about any environment on planet Earth, and even beyond. These assemblies serve a similar function to wire harnesses, including keeping wires and cables organized, but are designed for entirely different environments. Read on as we explore the many different elements that exist within the fascinating world of custom cable assemblies.
Cable Assemblies By Industry
Each industry where our custom cable assemblies will be employed has its own unique set of requirements that dictate the design issues our engineers love solving.
- Industrial - power and signal conductors running within the same cable assembly help industrial control systems (ICS) maintain smooth operations in an efficient, cost-effective manner. ICS are used to maintain critical infrastructure systems like water treatment facilities, power plants, public transportation, and airports and also are at the epicenter of almost all forms of manufacturing such as a beverage bottling facility. ICS provides nearly complete automation of regular operations and performance monitoring. To construct these complex systems requires keen engineering and specialized considerations like hermetically-sealed connectors, spot-on strain relief, and cable stops at just the right moment to ensure the system can operate cycle after cycle.
- Medical - because of their application, medical cable assemblies usually require special considerations like bio-sensitive connectors, implementing medical safety jacks, or using specific materials like TeflonⓇ or silicone. Unique circumstances require specialized considerations like strain reliefs to help limit the pull between a vital monitoring device and the patient, while simultaneously being accessible but out of the way of the medical staff. For the highly customized machines used in robotic-assisted microsurgery, incredibly complex cable assemblies must be produced to transmit absolutely precise data and power from the controller to the instruments. Meridian’s experience and extensive tool crib allows for faster design, prototyping, and manufacture of life-saving medical equipment.
- Telecommunications - custom cable assemblies in the telecom industry help to transit the power, data, and signal that empowers our society’s global connectivity. Telecommunications encompasses the entire realm of transmitting signs, words, images, sounds, and information of any nature by a wide range of different systems. Such a sweeping industry requires our engineers to have incredible adaptability when it comes to producing the perfect solution to the issue at hand.
- Military - cable and wiring assembly manufacturers in the military sphere know their products will be heavily used and relied upon in the harshest environments planet Earth has to offer. Preventing exposure to extreme heat or cold, salt, water, and corrosive oils are just some of the elements Meridian’s design team has to build into the custom cable assembly. These vital assemblies help our men and women in uniform to travel, communicate, navigate, and so much more as today’s military is more dependent on technology than ever before. These systems are simply too vital to ever fail prematurely so we incorporate incredibly strong components like KevlarⓇ or specialized mylar sheathing to protect the critical electronic systems our cable assemblies empower.
- Other - while our four main areas of focus are presented above, Meridian has produced custom cable assemblies for just about every conceivable industry covering the gamut from automobile manufacturing to retail security. Because of our specialization in prototyping, we have grown incredibly adept at finding the perfect solution to meet our client’s custom cable assembly needs, in a judicious and cost-effective manner, before ramping into full production.
Cable Assembly Design
The design of custom cable assemblies requires a multitude of decisions that will directly affect the functionality and lifespan of the system. Our design has to be exact in order to meet the demands the project has placed on us. Below are just some of the many different elements that come together to form a finished assembly.
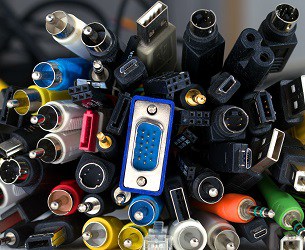
- CAD - at the onset, our design team will proficiently put to use a number of different computer-aided design (CAD) programs to map out the most efficient means to build the cable assembly’s myriad components. The design software can crunch numbers and permutations at incredible speed, vastly improving the time and accuracy of the different measurements required for the system to work correctly.
- Cable Types - acting as the building blocks for our custom cable assemblies, standard cable types help our engineers quickly put together the necessary components of a cable assembly design using products with known specifications. Standard cables such as TPT, SJOOW, STO, and SVEO can all be comprised of many different gauge configurations to meet the power, data, or signal (or combination thereof) requirements of the cable assembly.
- Connectors - far from solely being a junction for the cable to connect to a given source and destination, connectors come in an almost infinite variety and are used in an equal amount of applications. For example, military connectors are typically shorter in length with a low-profile design that helps increase the cable assemblies lifespan. Rectangular connectors have great lifespans and are incredibly reliable, yet are engineered to be lightweight and compact. These types of connectors are primarily used in industrial environments where a resistance to abrasion, flexing, and general impacts are required.
- Overmolding - overmolds are usually plastic and begin their lives in pellet form. The pellets have additions like colorants and fillers before being heated and injected into a mold. Overmolding offers protection, strain relief, can be used to increase flexure of a rigid part, or can help contain two pieces together without having to use some other fastener. Cable assemblies that are to be used in harsh environments greatly benefit from the use of overmolding.
- Junctions - in cable assembly manufacturing, a junction’s main responsibility is to shield the terminations they house from outside elements. Depending on the application, they can also be used to send power or signal from one location to multiple other locations or can be used to collect the control signals of input/output devices that need to arrive back at a control panel.
- Wraps/Shields - in most applications, the conductive wires within a cable assembly will require wrapping or shielding in order to prevent abrasion or interference. Interference occurs when an external source degrades or ceases a current, so our engineers build in “onboard avoidance systems” that allows the signal or current to transmit unimpeded. This is especially critical when the interference is intentional such as with radar jamming on the battlefield.
Cable Assembly Manufacturing
Once the design is in place and all of the different components have been decided upon, it’s time to begin the manufacturing process. Next, we’ll look at some of the various elements involved in producing a ready-to-roll cable assembly.
- Extruding - extrusion involves the different processes to make a cable assemblies cross sections. Uniformity of the cross sections are absolutely vital to the system’s integrity and prolonged functionality. An extruder machine is akin to a giant screw with a heated barrel. An attached hopper feeds the machine where the material is mixed and melted before being pumped into a die. Meridian can extrude conductors as small as 34 gauge all the way up to 12 gauge. The conductors make up the building blocks of the assembly and will be stranded depending on conductivity needs, then insulated, filled, wrapped, and shielded. Various connectors, overmolds, terminations, housings, and harnesses are used depending on the unique application the assembly is bound for.
- Prototyping Runs - one of Meridian’s greatest strength lies in our unique ability to do prototyping before ramping into full-scale production. In fact, more than 70% of the assemblies we produce were designed in house. Prototyping is like a practice before the big game. We’re able to see how the component sourcing is going to work based on things like pricing and availability and will often have to tweak the supply chain for optimality. Prototyping also allows the design team to reserve the correct tools needed for the job to run the assembly line. In the end, the use of prototyping allows for faster production runs (which translates to a more cost-effective process and better return for our client’s investment) when we go to full-scale production.
- Custom tool cribs - with more than 5,000 existing tools at our design team’s disposal, we have to have a great system for keeping track of everything. Behold, the tool crib. Tool cribs allow our team to know what tools are available for a given run and “check-out” the tools they need. Imagine having to stop an entire production run simply because the right tool wasn’t available when it was needed. A lot of our work is done by hand by truly skilled craftsmen but for the really intricate tasks we can use semi-automation or fully-automated machines to get the job done perfectly.
- Quality Assurance Testing - the pinnacle advantage of Meridian over a host of other cable assembly companies out there lies in the fact that every product we create undergoes multiple rounds of rigorous testing procedures. Prototyping provides an opportunity for a design to be tested for continuity, integrity, polarity, and functionality, and then to tweak the design as needed to optimize each; however, we will then retest 100% of the products that come off our assembly line to ensure the product works as designed for our clients. We maintain ISO 9001:2015 certification requiring a near-constant focus on quality assurance of both product, production, and customer service. Many off-the-shelf cable harness and custom cable manufacturers produce a one-size-fits-all product that may be spot, or batch-tested, so you never really know what you’re getting. Meridian uses automated Cirrus testers on most production runs and have custom built many functional testers depending on the unique requirements of the project. We even created our own “life testing lab” where components are tested in “real life” scenarios to ensure they can stand up to the rigors of the environment in which they will be employed.
Certifications for Cable Assembly Manufacturers
As discussed, Meridian is proud to maintain our ISO 9001:2015 certification. We also predominantly use UL-certified products and are a UL-approved production facility, both in the US and in our facilities in China. UL certification means our products have been independently verified for structural integrity, functionality, and, above all, safety. If you’re dealing with a custom cable assembly manufacturer that doesn’t use UL-certified products or isn’t UL-approved for manufacturing, you’re taking a huge risk with the components they produce.
Ready to Start Your Project’s Design Process?
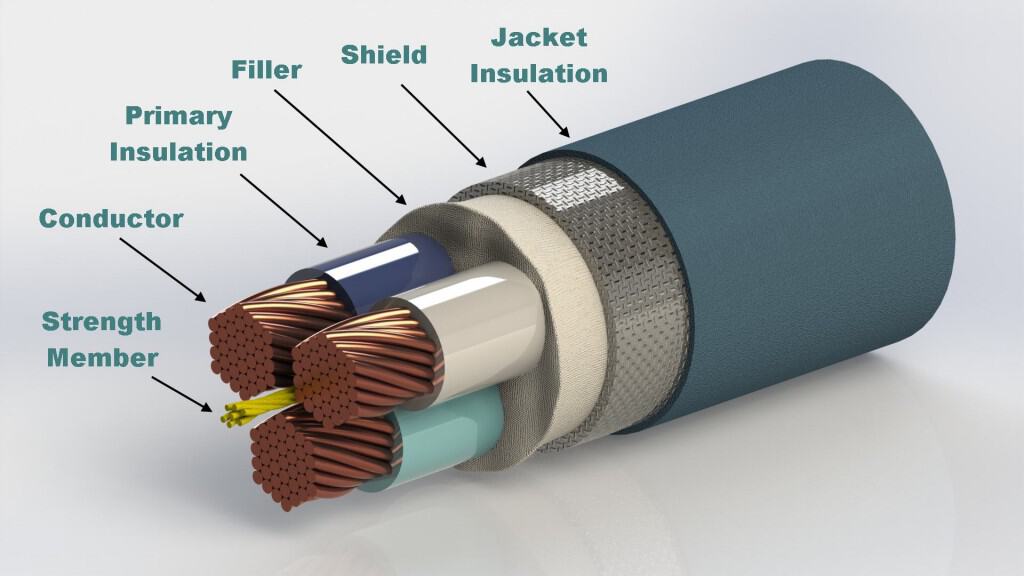
From the very first needs assessment with clients, through design, manufacturing prototypes, full-scale volume production, and final testing, Meridian’s team of professionals puts our client’s needs first. We’ll develop a product that works best given the constraints of the project. Period. We protect the investment made in us with a fanatical attention to detail to be able to bring together the most efficient use of our client’s budget. Our engineers love solving our client’s most complex problems in a judicious and creative way. When you’re ready to discuss your project’s unique demands, give our team a call at 1-877-806-8667 or use our convenient contact form.