Each component selected by a cable assemblies manufacturer affects the final performance of your finished product.
When designing or maintaining a piece of equipment, a lot can depend on the decisions made by your cable assemblies manufacturer. Selecting the wrong gauge for the wire or a jacketing material that’s inappropriate for the environment can, at best, cause the cable to fail prematurely, and at worst cause harm to people and damage to equipment.
The number of options available when designing a custom cable assembly can be daunting. The good news is that an experienced cable assemblies manufacturer will help you select components that make the most sense for your project. To help you get an idea of what to expect, we’ve covered a few of the common questions most common questions we get during the cable design and manufacturing process.
Where’s the best place to start when first talking to a cable assemblies manufacturer about a new project?
With any new custom cable project, it’s always best to start with clear communication about the specifications for your equipment and the environmental conditions where the cable will function. Your custom cable design team uses the information you give them to make decisions about each and every component of your cable assembly. The environment and needs of your equipment are weighed against your project’s budget to make the best choices for your custom cable assembly. The more details you can give, the better the performance of your finished product.
What questions will the design team ask at the beginning of the project?
You may not always know what information will be important, but don’t worry. If you’ve picked a cable assemblies manufacturer with extensive experience in the type of cable you need, they will know what questions to ask. A few of the common questions you may get are:
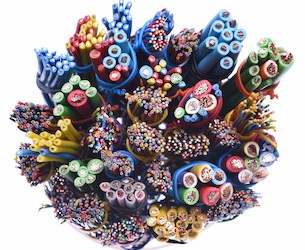
- Does the cable need to extend and retract?
- Is the standard use condition static or dynamic?
- Will the cable need to withstand extremes in temperature?
- Does the cable need to be cleaned or sterilized regularly?
- Will it be exposed to sunlight or moisture?
- What type of signal will the assembly carry? Power, data or a combination of both?
- What type of data will transmit through the assembly?
Should we use the best conductor, filler, jacketing, etc.?
When designing a custom cable, “best” can be subjective. For example, a solid conductor of a particular gauge might be able to handle the amount of current or signal required but be too brittle for the amount of twisting and flexing needed from the cable. Another example might be choosing an aramid fiber for the outer jacket because of its heat resistance, but the cable will function in a “wet” environment. Since aramids absorb moisture, it would need to be coated with another material to be waterproof. There may be a better material that is heat and water resistance that is more economical. The design team should be able to weigh the specifications to determine which is the best choice for your budget.
Conclusion
The many factors that go into choosing components for your custom cable can seem overwhelming if you don’t have a good working relationship and open communication with your cable assemblies manufacturer. The best way to get a quality finished product is to work with a team you trust and be prepared to share as much information as possible. Contact Meridian Cable when you’re ready to get started on your next custom cable project. Our team is happy to answer any of your questions.