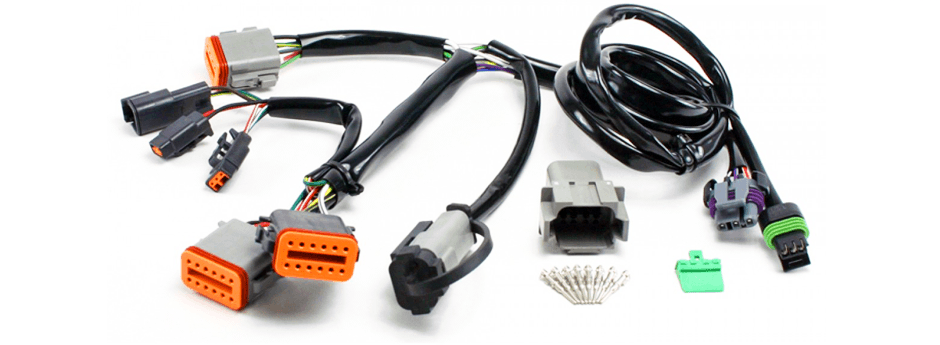
What do you think of when you hear the term “Wire Harness Assembly”? Like many, you may be inclined to picture a mechanism for organizing loose strands of cables or wires. While this description is partially correct, wire harness assemblies serve a much more useful purpose. Today’s blog post will dive into the world of wire harness assemblies.
Here, we’ll answer some of the most common questions related to wire harness assemblies. To do this, we will start from the beginning with its definition.
What is a Wire Harness Assembly?
At its most rudimentary level, a wire harness assembly is a collection of cables or wires that work together to relay electrical power or information and command signals. These cables and wires are often enveloped in a basic thermoplastic or thermoset casing to safeguard against external forces that would otherwise affect the structural integrity of exposed cables and wires.
By binding cables and wires into a single instrument, wire harness assemblies act as an organizational mechanism to diminish the amount of space that would have been otherwise taken up by singularly installed cables and wires.
The Benefits of Using a Wire Harness Assembly
Wire harness assemblies are important instruments in the operation of electrical systems around the world. They are often incorporated because they increase the efficiency of these systems. In this section, we discuss two of the major reasons why wire harness assemblies are popular: organization and protection.
Wire Harness Assemblies Save Valuable Space
Have you ever gone into the attic during the Christmas season to get your lights and found that the strands were hopelessly entangled? If you are one of the people who have experienced this event, then you can sympathize with how frustrating it can be to disentangle these from one another.
In applying the previous example to a collection of loose cables or wires, you will quickly understand the need for an organization mechanism. A disorganized system of interlocking and intersecting cables and wires can be equally, if not more, aggravating to work with than a loose collection of Christmas lights. This is especially true should the need arise to replace or rearrange dozens of cables and wires.
One of the major benefits of adopting a wire harness assembly is that it organizes your cable and wire arrangement. By clustering cables and wires beneath a single external casing, a wire harness organizes your cable/wire set up by decreasing the spatial dimensions needed to house the arrangement.
To illustrate this point further, consider the car that takes you to work or the airplane that flies you to your favorite vacation destination. Both the car and the airplane require thousands of feet of wiring to operate effectively and efficiently. So, instead of attaching an abundance of cables and wires separately, the wire harness assemblies group cables and wires into an individual apparatus that is then easily installed.
In short, if you are an individual that values organization and order, a wire harness assembly will change your life.
Wire Harness Assemblies Protect Cables and Wires
A wire harness assembly not only acts as an organizational tool but also protects the functionality and durability of your cables and wires. Interconnecting and intersecting cable and wire setups may result in suboptimal performance and damage to cables/wires over time. Organizing cables and wires using a wire harness assembly can minimize decreased functionality and potential damages resulting from external forces. More specifically, the outer thermoplastic or thermoset casing of the harness acts as a basic buffer against the negative impacts associated with moisture, lacerations, and accidental vibrations.
Additionally, wire harness assemblies can protect against electrical damage. The insulating sheath that covers the bound cables and wires assists in preventing electricity from shocking those working with them. Additionally, the possibility of an electrical short is diminished since the sheath that makes up the wire harness assembly grouping cables and wires are firmly bound.
Because wire harness assemblies provide organization and increase protection for the cables and wire, they are an important element in global electrical systems. The next section will illustrate how wire harness assemblies are utilized across various industries.
The Many Applications of Wire Harness Assemblies
Wire harness assemblies have many different applications. The list of applications extends across multiple industries and sectors including, but not limited to, the agriculture, automotive, communication, manufacturing, and medical sectors.
Agricultural Industries
Much of the equipment and vehicles used in today’s agricultural sector utilize wire harness assemblies. The organizational and protective features of wire harness assemblies ensure that heavy machinery, such as tractors and cultivators, operate throughout the year.
Automotive Sector
Wire harness assemblies are installed in cars to help disperse electricity and electric signals throughout the vehicle. The electric power and signals that pass through the wire harness are instrumental in starting the ignition, turning on the lights, cooling and heating the car, listening to the radio, and rolling down the windows.
Communications Systems
Global communication systems rely on wire harness assemblies to connect the world. From modems to routers and broadband networks to satellite receivers, wire harness assemblies are pertinent in powering the infrastructure that makes instantaneous communication possible.
Healthcare Technology
Modern medical care would arguably not be possible without the integration of wire harness assemblies into the devices used in doctor’s offices and hospitals to treat modern ailments. Medical instruments are often subject to frequent operation and must rely on the durability and versatility of wire harness assemblies to assist in maintaining functionality.
Industrial & Manufacturing
Wire harness assemblies are frequently used in the industrial control and manufacturing processes. As assembly line and production systems require intricate cable and wire systems to fuel automation, it is the wire harness assemblies that organize these elaborate connections of cables and wires to streamline the production process to ensure the optimization of the much larger manufacturing components.
All things considered, wire harnesses assemblies are a common feature found in electrical systems spanning the globe. Without them, modern technology would arguably not nearly be as efficient.
The Difference Between Wire Harness Assemblies and Cable Assemblies
One common assumption made about wire harness assemblies is that they are interchangeable with cable assemblies. Wire harness assemblies are often confused with cable assemblies because they both have similar features; however, they are not the same.
Wire Harness Assembly
As a short review, a wire harness assembly is a collection of bound cables and wires sheathed in a basic thermoplastic or thermoset material designed. The wire harness assembly sheath is simply designed to bring organization to the installation of cables and to provide basic protection from externalities. This basic construction defines wire harness assemblies as best suited for indoor use where externalities are minimal.
Cable Assembly
Similar to wire harness assemblies, cable assemblies consist of bound cables and wires. However, the material in which they are wrapped tends to be more durable. Cable assembly casings are usually made from materials, such as vinyl or thermoplastic rubber, that allow the unit to operate in the most intense environments where externalities abound. In comparison to wire harness assemblies, cable assemblies are often best suited for outdoor use or within environments operating under various amounts of stress, such as heat, moisture, and friction.
If you are interested in delving into the more intricate details of the differences between wire harness assemblies and cable assemblies, read our article entitled “Cable Assembly VS. Wire Harness”.
Designing a Wire Harness Assembly
Wire harness assemblies are often designed to meet the needs of a purchasing agent. Depending upon the customer’s specifications and energy requirements, the number of cables and wires in a wire harness assembly can vary. In its most elementary form, a wire harness assembly may contain only a few cables or wires with only the most necessary terminals installed.
On the other hand, for electrical systems that require a variety of operations and functions, a wire harness assembly may contain an incredible assortment of cables and wires that, without a harness, would resemble a never-ending labyrinth. In the end, the complexity of the design will ultimately be impacted by the function it is being designed to do. Meridian Cable specializes in designing simple to complex wire harness assemblies for a variety of purposes.
Getting the Perfect Wire Harness for Your Application
If you are in the market for a custom wire harness, Meridian is here to help. Our team is committed to creating the highest quality, customizable wire harness assemblies for our OEM customers. We have the capabilities to engineer wire harness assemblies for all types of applications. We guarantee that we will customize the perfect wire harness assembly to satisfy your necessary specifications. Alternatively, if you do not have a specific design in mind, we also maintain a large selection of pre-made products that are sure to meet your needs.
Check out our products page to view our full range of products and customization options available to you and contact our team to start reviewing your project’s specifications.