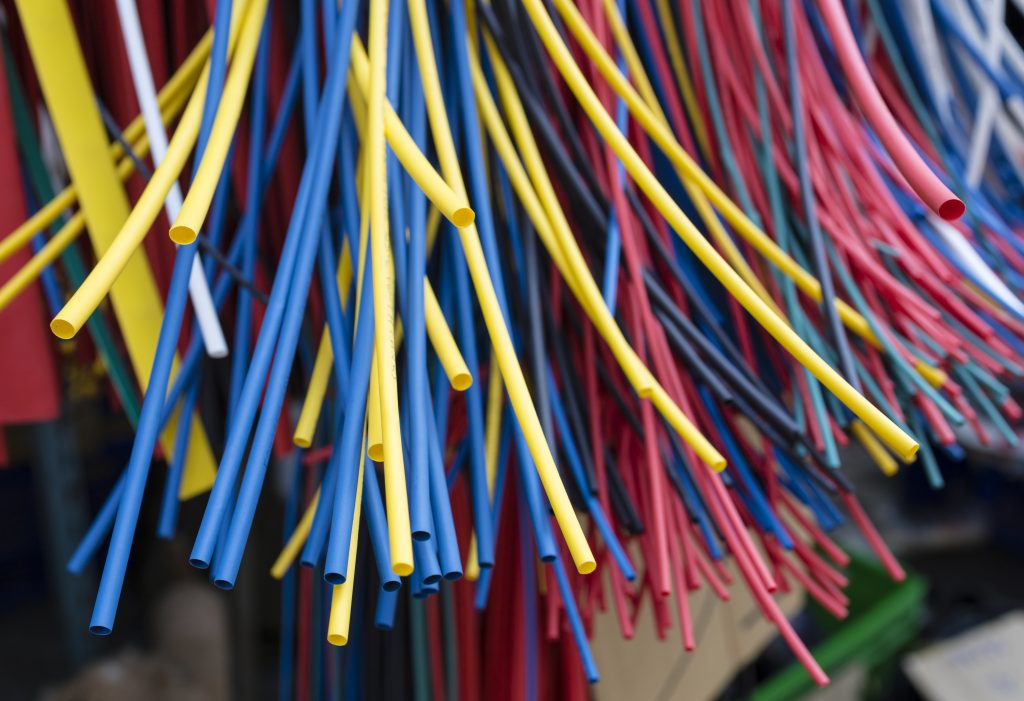
Heat shrinking tubing, aka heat shrink sleeves, are a simple, yet effective, means for providing a range of benefits that increase the useful lifespan of a given cable assembly. Made with various materials to fit the environment, heat shrinking tubing is a fantastic way to “beef up” assemblies.
In today’s LiveWire spotlight, we’re highlighting what makes these humble components so vital to a well-protected cable assembly and how adding them into your design can greatly increase the stoutness of the overall design.
Heat Shrink Tubing 101
In cable assembly manufacturer parlance, heat shrink tubing is a tube that can be made from any number of different materials which wraps over a wire, connector, joint, or terminal to provide more protection. The addition of heat shrinking tubing is meant to provide an additional shield against environmental variables and other physical forces. Moisture-resistance, abrasion-resistance, and increased insulation are all ancillary benefits of heat shrinking cable assemblies.
Heat shrinking sleeves work like this—the chosen material of a particular size, type, and thickness is inserted over a given component and then heat is applied to literally shrink the tube onto firm contact with the components beneath. The process of heat-shrinking creates an excellent seal and a tough outer shell for whatever element needs the added protection heat shrinking tubing provides.
Benefits of Using Heat Shrink Tubing and Sleeves in Cable Assemblies
A heat shrink tubing addition into your cable assembly design can be an absolute life-saver with the added protection provided. But these handy tools also bring about many other benefits to your overall cable assembly which produce value far and above the initial cost of utilizing them in your next cable assembly.
Heat Shrink Tubing Provides Additional Protection from Outside Forces
Hands down, the best usefulness for adding heat shrinking tubing to a cable assembly is to help protect the sensitive components from all the environmental variables that can degrade the transmission of data, power, or signal.
The heat shrinking tubing acts as an additional barrier to abrasions while also mitigating against liquids, humidity, and temperature swings. Depending on the material used in the heat shrink sleeves, the tubing can help the assembly’s components withstand extremely harsh environments, making it ideal for applications like aerospace and the military.
Heat Shrinking Tubing Provides Additional Insulation for Wires
Insulation plays a crucial role for protecting the conductors within the cables themselves. As above, different environmental factors like moisture, dust, temperature swings, acids and oils, and a host of other factors all need to be safeguarded against.
Our cable engineers take into account the application of the cable assembly to provide our clients with a design that is perfectly suited. Heat shrinking tubing provides an additional layer of insulation that helps maintain the integrity of the data, power, and/or signal that needs to be transmitted.
Heat Shrinking Provides Additional Strain Relief
An important element in any custom cable assembly is strain relief. One of the most important applications we’ve helped provide this for is within the medical field, where complex devices required extremely specific strain relief computations in order to provide a working unit. By utilizing additional means for strain relief such as with heat shrinking, our engineers are able to produce a clever solution to even the most complex issues facing our clients.
Strain occurs because the cables need to stretch and bend, often within confined environments. The tension can lead to premature wear, which can ultimately result in a failure of the system. Heat shrinking helps to reduce this stress by providing a mechanism for mechanical support.
Heat Shrink Sleeves Aid in Cable Cord Management
When you have a set of cables that are poorly managed, integration and maintenance can be a nightmare. Heat shrink sleeves help to bundle coordinated groups of cables together within a single, confined space. This provides a much cleaner finished product, as well as helps to serve as an effective wire management strategy.
What Is Heat Shrinking Tubing Made Out Of?
The material chosen for a heat shrinking tube in a cable assembly design is dependent on the needs of the project. Each material brings its own pros and cons, which our cable engineers carefully consider and weigh against the needs of the project.
Common materials used in heat shrinking tubing include the following and more:
- Polyolefin: this is one of the most prevalent materials used in heat shrinking tubing because it is extremely flexible, durable, shrinks quickly, and has built-in fire and UV resistance. Polyolefin heat shrinking also provides great protection and insulation properties.
- Polyvinyl Chloride (PVC): another great option for heat shrinking tubing is PVC. That’s because PVC is very affordable yet still offers a solid level of protection. PVC is a very common material to use for its heat, moisture, and abrasion-resistant qualities.
- Polytetrafluoroethylene (PTFE): commonly referred to as “Teflon®”, PTFE is a very strong and nonflammable synthetic resin compound. Known for its versatility, PTFE offers a high-performance material choice for mitigating against temperature swings, moisture, abrasion, and other variables.
- Fluorinated Ethylene Propylene (FEP): great for use with injection molding and extrusion, this variant of Teflon® is also a bit easier to work with. FEP also carries low-friction and reactivity properties, making it ideal for sensitive electrical components.
- Polyvinylidene Difluoride (PVDF): PVDF is a special form of plastic that’s able to be injected and molded with ease. This product has great heat-resistance and chemical resistance making it well suited for tough environments such as with the military and telecommunications industries.
- Silicon: silicone rubber provides one of the best protections against temperature swings with an excellent thermal range. Silicone resists heat well and is also maneuverable and flexible, making it an ideal choice when spaces are tight. Silicone is also very easy to disinfect, which is why it’s often used in the medical field.
Believe it or not, there are even more types of materials that can be used for heat shrinking tubing. It really all depends on the application and the needs of the project. Once we’ve established the specifications, our cable engineers work to design a product that’s perfectly suited for the application. We’ll then test and retest the prototype within real-world conditions to make sure everything functions absolutely on-par with expectations.
Making the Perfect-Sized Heat Shrinking Tubing for Your Cable Assembly
The three most important measurements to watch for when choosing the right heat shrinking tube for a cable assembly include the inside diameter of the tube, the tube’s ratio for shrinking, and the overall length of the tube.
Determining the Inner Diameter of Heat Shrinking Tubing:
When you’re looking at the diameter of the tube, we’re talking about the inside lining. To adequately cover the components that need protecting, you’ll need to consider the total area of the components. This is performed by giving enough allowance for the heat shrinking process, while also ensuring a tight seal.
Considering the Heat Shrinking Tubing’s Shrinkage Ratio:
There are many different common ratios out there for given materials used in heat shrinking tubing. Having UL-certified components from the get-go allows our cable engineers to work with products with known specifications and which have been tested for quality. With a heat shrinking ratio that says, for example, 2 to 1, you’re looking at a tube that’s going to shrink down to 50% of its starting size. Different-sized components such as a connector versus a stranded wire, are going to have different needs for adequate coverage.
Choosing the Right Length & Thickness Heat Shrinking Tubing:
You also need to remember that the length of the tubing, as well as the thickness will be moving variables as the heat shrinking takes place. The length of the tubing can be reduced by almost 10% with some materials, meaning you should always have a greater length than what’s getting protected. Conversely, with heat shrinking tube thickness, you’re actually increasing the thickness of the tubing as it gets smaller.
These variables require careful consideration during the design phase, and will be tested for durability, continuity, and functionality during the testing and/or prototyping phases.
How to Ensure Quality with Heat Shrinking Tubing
The best way to ensure quality with heat shrinking tubing is to go with a reputable manufacturer who has credentials from UL and ISO. We’re honored to hold certifications as a UL-approved manufacturing facility, as well as to maintain our ISO 9001:2015 certification for our persistent obsession with quality in every facet of the manufacturing process. When quality meets experience and capability, the result is a far superior product for our client and the end user.
Adding Heat Shrinking On Your Custom Cable Assembly
At Meridian, decades as leaders in custom cable assembly has helped us build a large collection of custom tools and equipment in order to produce the one-of-a-kind products our clients know they can depend on.
Ready to add heat shrinking tubing to your design specs? Contact our team now and we’ll help to review all the considerations for your unique design.