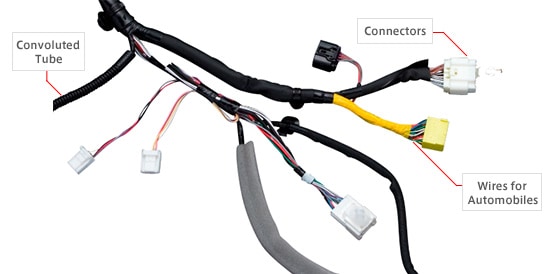
With over 5,000 existing tools at our disposal, chances are good we’ve got everything we need to produce even highly complex and completely customized solutions. However, there are many instances where we’ve had to design a totally new tool or testing mechanism when a solution is a never-before-seen amalgamation. We leverage decades in the industry to produce products for our clients that we know will stand up to whatever application they will be utilized in and also can be delivered within a viable framework, given the time and budget constraints of the project.
Aerospace, automotive, lighting, and alternative energy are just some of the many different industries we stand ready to serve with our custom solutions to even the most complex problems our clients present us with. While solving problems is something our design engineers are really good at, the solutions are only viable if all the pieces of design and production can meet both the budget and timeline set forth for the project. With strict adherence to kanban manufacturing techniques, just-in-time ordering, and efficient, worldwide logistical support, we are able to deliver full-functional and repeatedly-tested cable assemblies and wire harnesses to clients anywhere in the world.
Cable Harness Assembly Design and Manufacturing
Our design and manufacturing process follows a set protocol towards maximizing a project’s budget, meeting project milestones and ensuring the absolute functionality of the final product. Here’s a quick snapshot of a few key elements of the process:
- Needs Assessment: we will examine all of the specifications for your project and seek to understand all of the elements at play for how and where the system will be employed. This is where initial design elements are started to be placed together which will later be developed into working prototypes.
- Extruding: our in-house extruding machine can extrude conductors as small as 34 gauge and all the way up to 12 gauge. These conductors make up the building blocks of both cable assemblies and wire harnesses. They can be stranded or braided, filled with insulation, wraps, shields, and other components depending on the project needs. Connectors, overmolds, terminations, and housings help bring the cables and wires together within an electronic system.
- Prototyping runs: we will usually produce several iterations to not only test a unique combination of components for accomplishing a given task, but will also look at how those components are sourced to see if a given assembly is viable.
Why Certifications Matter
One of Meridian’s greatest strengths lies in our Quality Assurance program. Each and every product that rolls off our assembly line will be tested through multiple iterations to ensure continuity, integrity, polarity, and functionality. Prototyping allows our design staff to gauge different configurations and sourcing in order to find the most efficient means of solving the problem at hand.
Maintaining an ISO 9001:2015 is no easy task and certification to which we are extremely proud to have held for nearly 20 years. ISO 9001:2015 requires a company to demonstrate they have advanced quality assurance processes in place and also mechanisms for continual improvement in both product and production, but customer service as well. Additionally, we are an Underwriters Laboratory (UL) certified production facility and predominantly use UL-certified components. UL certification means our products have been independently-verified for structural integrity, functionality, and safety. This allows our design staff to utilize a component with a known specification, that’s been stringently tested, rather than creating a whole new component from scratch.
If your cable or wire harness supplier isn’t ISO certified and doesn’t utilize UL-certified components, they have not made a solid commitment to quality assurance and you will be taking a huge risk with the products they produce.
Cable Harness Assemblies for Industrial Controls
Industrial control systems, or industrial process controls, require a complex array of signals, data, and power to be sent at just the right time in the production process in order to provide the intended function. These systems provide almost complete automation for the operations and performance monitoring functions within many critical infrastructure systems like water, power, and civil transportation systems, as well as in manufacturing settings like a bottling plant.
Meridian’s custom-built wiring harness and cable assemblies provide the necessary infrastructure for these process controllers to perform at their best. Particular considerations for industrial control systems include incorporating components that ensure the fidelity of the process. For example, engineering in radio frequency interference (RFI) avoidance measures, which can include specialized shielding, helps to avoid costly delays within an industrial control system when a wrong signal is sent/received and causes some crucial function to not be performed. Even small delays in an industrial setting can be incredibly costly. Hermetically-sealed connectors, strain reliefs, and cable stops are all utilized to ensure the system operates as intended cycle after cycle.
Cable Harness Assemblies for the Military
Cable harnessing companies operating in support of providing our military with crucial electronic systems components knows their products will more than likely be deployed in some pretty extreme environments. Not only must they contend with extreme temperature swings, sand, dirt, dust, and mud, but also exposure to water, salt, and corrosive materials must be accounted for in the cable assemblies and wiring harnesses being used for military purposes. Our men and women in uniform count on our products to assist them in everything from navigation to communication, and increasingly are being utilized to empower unmanned systems such as UAVs. Special considerations in design can include incorporating Kevlar into the sheathing material to prevent cutting and aluminized mylar to prevent interference.
In support of their mission, our design team comes together to produce a solution that works within the usually tough parameters set forth by our clients in military contracting. We are adept at meeting project and budgetary milestones to deliver the perfect solution to the complex problem at hand.
Cable Harness Assemblies for Other Industries
Aerospace, automotive, lighting, and alternative energy are just some of the many different industries we stand ready to serve with our custom solutions to even the most complex problems our clients present us with. While solving problems is something our design engineers are really good at, the solutions are only viable if all the pieces of design and production can meet both the budget and timeline set forth for the project. With strict adherence to kanban manufacturing techniques, just-in-time ordering, and efficient, worldwide logistical support, we are able to deliver full-functional and repeatedly-tested cable assemblies and wire harnesses to clients anywhere in the world.
Ready to Go Over Your Project Specs?
Our team stands ready to review your project’s unique specifications and will deliver a solution perfectly suited to match your needs. Contact us now to start the design process.