Custom Wire Harness Manufacturer - It’s Who We Are
Wiring harnesses are the crucial workhorses of our modern, connected society. These marvels of advanced engineering require many hours of precise design, production, and testing in order to provide our clients with a solution that works—no matter what. At Meridian, high-quality, custom wire harness assemblies is what we do and what we’ve done for decades. We’ve built an incredible knowledge center of top talent, an extensive tool crib, and a sophisticated network of fully-automated and semi-automated systems, as well as hand tools, to create some of the most state-of-the-art cable harness fabrications.
What is a Custom Wire Harness?
At its core, a wire harness is simply a group of wires and/or cables, often with their own sub-assemblies, utilized for transmitting power, data, or signal through an electrical system. Often, the complex wire harnesses we create for different industries like telecommunications, military applications, medical, industrial controls, and more, require multiple connectors, strain reliefs, grommets, and other components to efficiently fulfill the needs of the system.
At Meridian, it doesn’t matter if there are dozens of mixed-gauge wires, scores of connectors, or dozens of terminations, we have the knowledge, skills, and ability to complete each custom wire harness design project to perfection on time and on budget.
How the Custom Wire Harness Assemblies Process Works
The wire harness assemblies we create here at Meridian are engineered to fit perfectly within their intended environment. That means making sure the design fits geometrically and within the specifications required of the system. Whether it's for an industrial control system in a busy bottling facility or the OEM wire harnesses required in the automotive sector, the idea of “fit” is crucial in wire harness design.
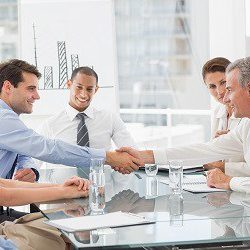
Custom Wire Harness Fabrication Process
As a UL-approved manufacturing facility, we utilize many standard UL® cable types. This allows our team to start with a cable with known specifications and utilize its strengths to our client's advantage in the assembly process. How that process is played out will vary from one project to the next as each has its own unique set of specifications based on the intended application.
However, a typical wire harness assembly can include:
- Affixing wires, sub-assemblies, and other components directly to a pinboard.
- Navigating all of these components through the necessary cable sleeves for added strength and protection.
- Make sure any cable ties, cable wraps, or other infrastructure is secured and in its right place, paying particular attention to critical branch-out locations.
- Utilizing automated, semi-automated, or even hand crimping tools for wires especially when we have multiple wires into single terminals.
By having fully-automated and semi-automated capabilities, alongside our production team’s highly-skilled use of hand tools, we’re able to blend technology and fine work craft in a single, perfect package. Hand tools are still quite necessary, even in our state-of-the-art production facilities, in order to pull off a successful project.
Some of the processes which require both hands-on attention and automated solutions include:
- Precise cutting and stripping wires.
- Automated crimping for terminals.
- Utilizing fine pitch, computer-controlled soldering.
- Ultrasonic welding.
- Overmolding to strengthen and protect connectors, strain reliefs, etc.
Wire Harness Design Starts with the Right Components
Wire harnesses are able to facilitate the manufacture of larger systems by providing the critical connections needed in a “plug and play” install. But don’t let that name fool you, while there are universal wiring harnesses, these are often generic solutions that may check some, but not all of the boxes required in a unique application. Our cable harness design engineers work hard to create the perfect amalgamation of conductors, wrapping, sheathing, connectors, strain reliefs, grommets, and all other components required.
In addition to the perfect materials, we also have to take into account the intended environment. Protecting against abrasion, caustic chemicals, moisture, dust, interference, and any number of additional environmental variables is absolutely crucial for ensuring long-term operability.
Designing in a Virtual Space Allows 3-D Renderings & Simulation
Once we examine the variables at play and have a good idea of the specs required, our design engineers get to work using our advanced computer-aided design (CAD) software. These sophisticated digital design systems afford our engineers a chance to piece together individual components with incredible precision and even test them in various simulations, all in a virtual space before the first cable is extruded. Putting in more time upfront streamlines the entire production process, which is a tenet of our ISO 9001:2015 certification, which prioritizes operational efficiency across the entire organization.
Prototyping Wire Harness Assemblies is a Huge Advantage
Once the design is just right in the digital space, it’s time to see how the components come together in the real world. We have the ability to prototype different configurations, including cable assembly prototypes, for qualification samples to help ensure we have the perfect combination of components, materials, and processes. Our wire harness engineers utilize the schematics our brilliant design team developed to map out the assembly board to be used for the wiring harness.
An assembly board (also referred to as a pinboard) is a life-size diagram for the wiring harness, showing our skilled production team just where each component is meant to go. From a process standpoint, the pinboard is basically a workbench for physically building a wire harness assembly. Each and every wire for the project is cut to the perfect length and detailed identification is used to keep everything in its proper place. From there, we’ll often strip wires to showcase the conductor beneath and make it ready for its accompanying connector or terminal. All of the necessary components are held in place by a complex network of cable sleeves, ties, and other infrastructure to make sure it's a rock-solid system.
Prototyping allows our team to analyze how several different versions compare when brought together in real-time and tested under real-world conditions. From there, we can select the most advantageous iteration to move forward with volume production, saving both time and money down the line.
Custom Wire Harnesses Proof Points
We offer such highly-customizable features with each and every wire harness we produce such as:
- Conductor Sizes
- Conductor Colors
- Stranding Sizes
- Conductor Colors
- Materials
- UL-Certified Wires and Cables
Utilizing the best components in each application means our clients get a product they know they can depend on, cycle after cycle. When you’re operating in high-stakes industries like global telecommunications, advanced medical technology, with our military, and a whole host of other mission-critical industries, your solutions have to work, period. That’s what Meridian brings to the table with our many years of offering custom wire harnesses that are depended on to get the job done every day.
Testing is Everything to Consistently Ensure High-Quality Wire Harnesses
Once every aspect of the wire harness design process comes together, the absolutely pivotal process of testing begins in earnest. Each and every wire harness we produce will be 100% tested for continuity, integrity, polarity, and functionality before shipping to our clients around the world. We created an Advanced Life Testing Lab where we can test our products under the harshest real-world conditions imaginable.
We utilize a suite of different testing systems that can detect even the smallest irregularities in a wire harness design so our engineers can make sure it's right before it leaves our facility. Investing in state-of-the-art testing equipment means we have complete control over our quality assurance and quality control (QAQC) processes.
In the end, this attention to detail in quality stands at the heart of everything we do here at Meridian. The Advanced Life Testing Lab also helps our team qualify new designs which can help when our client desires to get their product certified through a certification agency like UL.
How to Start a Wire Harness Design Project
Offering full-scale wire harness and cable assembly design and engineering services means we can deliver the perfect solution on time and on budget, every time. We have honed our process over decades and built our capabilities to be agile enough to respond to changing project needs. The entire process starts with a detailed conversation with our clients to review the specifications required to meet their needs. This strategic conversation allows our project managers the opportunity to map out a timeline, reserve tools in the tool crib, and ensure all the pieces are in place to complete a successful project. Our team is composed of highly-experienced professionals who are skilled innovation makers. When you’re ready to get started, you can contact our team however is most convenient to fill out the quick online contact form on this page, calling us at 1-877-806-8667, or emailing our team at sales@meridiancableassemblies.com.
Ready to find out more?
Drop us a line today for a free quote!
Custom Wire Harness FAQs
Get information on how Merdian Cable Assemblies creates a custom wire harness. We supply wire harnesses all over the USA and answer the most commonly asked questions from how we create a custom wire harness to fit your needs to providing information on what wire harness manufacturers actually do. Read on for more information and feel free to contact us directly for any questions that you might have.