Collaborating with a custom cable manufacturer to produce durable wiring that meets your product’s specifications.
Like the majority of industrial products, wiring systems must also be designed and maintained properly in order to withstand harsh conditions. If these products are not looked after and properly attended to, the results can be negative–resulting in a large piece of machinery breaking down and causing delays, or something as catastrophic as a fire. To avoid many of the issues that can result from damaged wiring, it is important to gain an understanding of the customization that your product’s wiring requires and of any maintenance that may be needed. The best place to get this information will likely be from your product’s wire and cable manufacturer. When discussing this, there are a few key elements to keep in mind:
Protecting Your Custom Wiring From Corrosion
The majority of wiring is made of copper, which is susceptible to corrosion when used in harsh or damp conditions. Cables that will be buried, for example, must be coated in a thick jacketing that can withstand conditions underground. Aside from this jacketing, this type of wire must also be sealed so that the soil and any materials in it cannot damage the inner conductor.
Water can also corrode copper over time and most of us have seen the green and white residue that often forms on copper pipes. The wiring’s proximity to water should be considered and addressed by your wiring manufacturer. Specialized techniques can be applied in these instances, particularly if the wiring will come into contact with salt water. When possible, wiring that encounters such conditions should be inspected regularly for signs of damage to the jacketing and residue building up around connectors. Damaged wiring, or wiring that shows signs of corrosion, must be repaired to ensure that it continues to function optimally.
The Right Jacketing Material For Your Custom Wiring
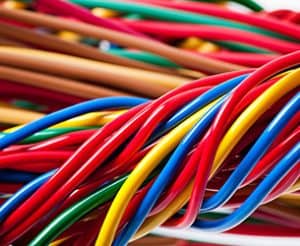
Designing and Maintaining Your Product’s Customized Wiring
The proper jacketing can be the difference between a long-lasting wiring system and a system that falters. With the proper jacketing, a wiring system should be able to withstand and protect the wiring’s vital conductors from damage resulting from motion, environmental factors including animals and insects, and water if necessary. There are so many additional factors that can alter a wiring system’s functionality that it is important to work with an experienced wire manufacturer who understands your industry and product.
Armed with an understanding of your product and its functionality, your cabling manufacturer should be able to choose an appropriate material that will reduce the wear and tear on your product, minimizing the amount of maintenance that it will require. Contrary to what many assume, there are many types of wire jacketing available to protect your product’s wiring system. This jacketing can be made so that it is resistant to cuts and UV rays, crafted so that it is resistant to high temperatures, and more. The innovation in this industry means that you are sure to find a product that is ideal for your custom wiring needs.
Because of the crucial role that wiring plays in modern machinery and communication, it is important that the wiring you choose to utilize is reliable. To ensure that you are receiving high quality wiring that will last, talk to your manufacturer about the options that are available and the level of specialization that your product or industry demands.