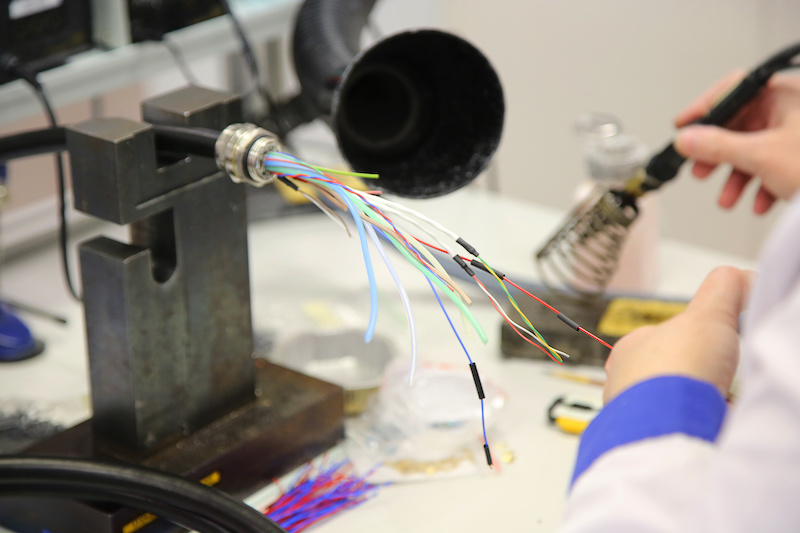
Ever find an absolutely perfect cable assembly only to find out you can’t get it anymore because the item has been discontinued? Or perhaps you’ve seen a custom cable assembly in action elsewhere and would love to emulate something similar with your own set-up. However you’ve arrived at this situation, the good news is that there’s a solution to get you the same product perfectly matched to your desired specifications.
Today’s LiveWire News spotlight will dive into the process of reverse engineering and how our cable engineers can use this approach to reproduce a perfect match of your existing cable assemblies.
What is Reverse Engineering?
Reverse engineering is the process of deconstructing another product piece by piece in order to reproduce that same product in exacting detail. Reverse engineering can be applied to a wide array of industries—everything from aviation to auto parts and anywhere in between. That’s because reverse engineering is nothing new.
As manufacturers have come to rely on large pieces of machinery in order to produce a given product, a lot of capital is required in order to get the right machines in place. As this equipment wears down, the original manufacturer may be long out of business or simply no longer producing replacement parts. The dilemma becomes do you throw out the entire piece of expensive machinery or can you reverse engineer a given component to keep the machine online.
Cable assemblies are an integral part of an untold number of different systems. Telecommunications, military equipment, medical devices, and so many more all rely on cable assemblies in order to provide their function. When new parts are difficult, if not impossible, to source, reverse engineering provides an excellent solution.
How Reverse Engineering Works
Reverse engineering is also referred to as “back engineering” because engineers are literally working backwards through the original manufacturing process to uncover the entire design. This may sound simple, but without the original methods used to construct each of the exacting details in something like a complex custom cable assembly, the process can be somewhat challenging.
Understanding the Original Design
With cable assembly reverse engineering, our cable engineers take each piece of the original product apart in order to garner a better picture of the original method of design and manufacture.
Meridian is all about quality in cable assemblies, designing and producing from the very first strand of wire onward to what can be incredibly complex systems. When we undertake a typical cable assembly design project, we start with the best components and build on each layer as required by our clients’ specifications. Reverse engineering is essentially this process in reverse.
Keeping Legacy Systems in Operation
If a client has an older piece of electronics equipment, say being used in an industrial control system, over time functionality can be lost due to advancements in technology. Reverse engineering helps our team uncover how these systems functioned and what all is needed to make them current. This sort of bridgegap can be incredibly cost-saving over needing to go out and purchase a whole new piece of machinery.
Sometimes, we may need to develop a new component simultaneously in order for the older systems to “talk” to newer systems. Reverse engineering can also be used to rediscover data or best practices that were used in the past but may have been lost over time.
Recapturing Intellectual Property
In terms of proprietary information, this process can prove invaluable. Before the age of CAD drawings and cloud storage, good old paper blueprints were used. Through an untold number of different scenarios, these documents could be lost and along with them the proprietary knowledge built into the specific component. Reverse engineering can help uncover these along the way. The process itself can also help to create new designs that perfect an older, less efficient design or to make the assembly fit within an updated system.
Reverse Engineering on Existing Cable Assemblies
To reverse engineer a custom cable assembly, Meridian simply needs a sample or, in some cases, even just a picture of the part in order to see how it works. Seeing how the cable assembly was integrated within an electrical system provides a fairly good starting point for how the assembly was utilized.
The cable assemblies reverse engineering process will definitely differ from assembly to assembly but, in general, we’re able to follow a few standard steps in the process including:
- Start with dimensions. When you’re starting with a cable assembly that needs to be reverse engineered, it’s a good first step to start with careful measurements. You may have heard the adage in construction “measure twice, cut once”, well, this same approach can be said in a reverse engineering cable assembly project.
Taking careful measurements and analysis, our engineers pour over all of the components of the assembly like connectors, terminations, wire lengths, types, and a thousand and one others in order to determine the signal, data, or power capacity present within the existing system. Utilizing technology like sensitive 3D scanners makes this process faster and more exact than ever before.
- Utilize CAD drawings. With a mountain of data at our disposal, Meridian’s cable engineers can then use sophisticated CAD software to develop even more detailed renderings of the cable assembly. CAD helps to create a 3D representation of the product where further analysis can take place. We’re also able to put the assembly through modeling software to better determine how the system was utilized.
- Identify components. Understanding the layout of the cable assembly takes understanding how each component interacts with one another and with the electrical system as a whole. Our engineers take special care to document all of these components as they were used in the assembly in order to facilitate rebuilding the new one.
- Disassemble the assembly. Taking care to minimize damage to each of the components, our team works to remove the various components of the assembly layer-by-layer. Starting usually with the outer shield or sheath, we’ll carefully strip back the componetns like a geologist examines substrate in the Earth. Each aspect needs to be kept extremely organized and kept in a logical order to better understand how the cable assembly functioned. As well, these components will be measured and analyzed to provide better data for the re-engineered assembly.
- Rebuild the new custom cable assembly. With all of the data made available while reverse engineering cable assemblies in hand, our engineers can then set to work producing the new cable assembly. As with every assembly we produce, the final assembly is tested for continuity, integrity, functionality, and safety to see if the new cable assembly will provide the necessary functionality for which it is intended.
While the process can be tedious, reverse engineering custom cable assemblies needs to be incredibly exact in order to preserve functionality. The cable engineers of Meridian rely on our massive tooling inventory in order to replicate a perfectly functioning copy of the cable assembly required.
Why is Reverse Engineering Cable Assemblies So Useful?
Reverse engineering can be incredibly useful for recreating the exact match needed to fit perfectly into an existing electrical system. However, the process itself provides ancillary benefits that contribute significant value to the overall effort.
- OEM Parts Replacement
When you have a key component like a cable assembly fail that is part of a larger system, it becomes critical to be able to replace that part to keep the system in operation. But an OEM may no longer make the part or is simply out-of-business. Reverse engineering helps bypass having a huge capital expenditure to replace an entire system by recreating an exact match of the OEM part.
- Repair and Replacement Knowledge
When a manufacturer is no longer producing a given cable assembly, the knowledge of how the product was utilized, correct repair procedures, and the necessary replacement parts may all be lost. Reverse engineering helps to recreate this intrinsic knowledge which helps if a similar issue were to ever occur in the future.
- Analyzing Points of Failure (POF)
Reverse engineering also helps our engineers have time to pour over the entirety of the cable assemblies design. Along the way, they may be able to pick up on why the components failed in the first place and ensure systems are in place to prevent this from reoccurring.
- Improving Components
Echoing POF analysis, our cable engineers may find certain aspects of the cable assemblies design are lacking or not quite as good as they could be. Reverse engineering affords the opportunity to improve upon any noted deficiencies.
Reverse engineering is a very useful tool in a custom cable manufacturers tool belt and a service we’re proud to offer our clients.
Need to Reverse Engineer Your Existing Cable Assemblies?
With the cable assembly in hand that needs to be replicated or even with just a picture, the gifted men and women of Meridian can reverse engineer your existing cable assemblies for even the most complex applications. Contact our team now to get your new custom cable project started.