The coil cord design process is not complete until proper testing has been performed.
The purpose of designing a coil cord instead of using a non-coiled cord is the added flexibility and durability it offers. In many cases, these types of cords are used in harsh environments with the expectation that they can be stretched and retracted over and over again without failing prematurely. The best way to make sure your completed cable performs as expected is by making thorough testing a part of the coil cord design process.
Advanced Life Testing in Coil Cord Design
Just as with other types of custom cables, engineers can select the right components of a coil cord to match the equipment and environment where the completed product will function. The final decisions for conductor, insulation and jacketing materials, and types of connectors should all be based on a careful review of information that weighs environmental conditions, technical specifications, and cost to produce. However, there are a few additional considerations when designing a coil cord.
The curly part of a coil cord is what sets it apart from other types of custom cables. It’s what allows the cable to retract to a resting length that is more compact than it’s fully extended length. This characteristic means additional care must be taken to make sure the cable performs for as long as expected. There are a few tests that can help the design team understand if they’ve hit the mark.
Cycles to Failure Test
Cycles to failure is the number of times a cable can be stretched and retracted before stress causes it to fail. To get an idea of when failure can occur with a newly created cable, we use a cycles to failure test. To test, a coil cord is connected to a test machine. The machine is then programmed with the cord’s extension length, cycle speed, and the length of time to spend retracted and fully extended, which are determined using the expected usage of the final product. We would then set the machine to cycle until the cord fails.
Retraction Compliance Test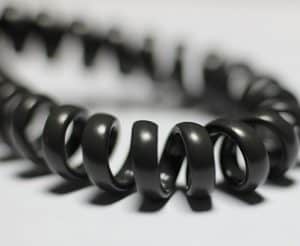
In this type of test, we are trying to determine the retraction compliance of a coil cord design. Retraction compliance is a percentage of the cycled retracted length to the initial retracted length. During the test, the resting cable is measured. Then it is cycled, allowed to rest, and then cycled again before being measured again. If the design is poor or the cable was very heavily cycled, the percentage can be in the 50% range. Well-designed assemblies can measure at 95% or more.
Cable Flexing to Failure Test
When we need to make sure a raw cable can stand up to fatigue, we use a cable flexing to failure test. After the cord is connected, the flexing machine is set to test the flex radius, rotation angle, and cycle speed. Once the settings are selected, the machine cycles the cable until the circuit is broken.
Conclusion
Testing your coil cord design in a lab during the production process results in fewer unexpected failures in the field. That means you get a safer product that will ultimately save you money. Get in touch with the team at Meridian Cable when you are ready to discuss your next custom coil cord project.