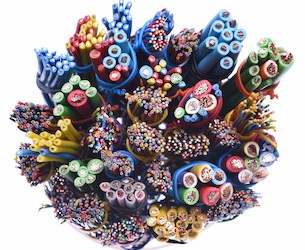
Custom cable assemblies are manufactured to be exact, specific to their purpose in a virtually limitless amount of different configurations. While our designers and engineers are some of the best in the industry, completing a one-of-a-kind custom cable assembly takes thousands of minute details in order to perform flawlessly under real world conditions. Getting from concept to final product can be a challenge, but our team has proven time and again, no matter how complex or demanding the project may be, we have the experience, tools, and capacity to pull it off flawlessly.
Here we’ll explore what makes custom cable assemblies so complex and how a custom cable manufacturer can be a value-added partner in your project’s success.
Complexities of Custom Cable Assemblies
Providing full product lifecycle services, our team has to be intimately aware of a thousand different considerations simultaneously in order to produce the best product possible. What makes cable design so complex as there is rarely ever two situations that are entirely the same. Even when the data, singal, or power transmission requirements are similar, the environmental variables that our custom cable assemblies will encounter during their lifespans is hard to replicate exactly so require a custom solution.
Several key areas help us control the vast amount of different processes needed in order to go from the client’s need we are presented with to a fully-functioning cable assembly performing its function in the field.
- Design: bringing together state-of-the-art design software that lets us model an entire system in a virtual environment as well as truly gifted designers and engineers gives us incredible capacity as tough problem solvers. Our design team loves a challenge. Need a molded component rugged enough for sub-zero temperatures? We’ve done it. Need a bio-connector with built-in strain reliefs for specialized medical equipment? We’ve done that too.
The design phase allows our elite team of proven cable design professionals the opportunity to compute vast amounts of data and different permutations in order to put together whatever is needed from the batch. This may be qualification samples, prototype iterations, or even full scale volume manufacturing. However, it is indeed rare to go straight from design to volume manufacturing without several rounds of prototyping in between.
- Sourcing: Meridian cable is a UL-approved production facility and we use UL-certified components in all of our products. We have the capacity to source components in a manner consistent with just-in-time ordering in order to be as efficient in our manufacturing process as possible. During prototype runs, we are able to compare different sourcing combinations in order to see which iteration will produce the most efficient production run. This level of detail is a huge advantage to using a custom cable assembly manufacturer in your project as your budget is able to be more effectively allocated.
- Prototyping: prototyping allows our design team to produce several different versions of the same product in order to test every aspect of manufacturing. We want the production run to be smooth and prototyping allows us to compare how each phase comes together. This includes looking at how different designs come together with different sourcing plans and which tools are right for the job. Prototyping also allows for a significant amount of product testing early on in the product’s development. This can help us avoid unnecessary delays further down the line.
- Testing: we follow incredibly rigid quality assurance and quality control procedures that we have honed after decades as leaders in the custom cable assembly manufacturing industry. Our almost fanatical attention to detail means each and every product that rolls off our assembly line has undergone multiple rounds of intense testing to ensure continuity, integrity, polarity, and functionality. We use stout Cirrus automated testers for the majority of production runs but have on many occasions produced a custom testing set-up when the product is something entirely new. Our testing procedures follow strict ISO 9001:2015 certification standards.
- Volume Manufacturing: Before going into full volume manufacturing mode, our design team uses project management tools like the critical path method to begin mapping out the activities needed to complete the project in the most efficient means possible. Volume manufacturing may sound like a brute force attack but in reality it takes many steps all in it’s own in order to run efficiently. Following Kanban manufacturing principles helps us remove waste from our production runs.
Other lean operations tactics like the just-in-time ordering mindset we covered earlier all help our volume manufacturing occur in as systematic and ordered fashion. We have well over 5,000 existing tools, overmolds, connectors, and other components we have built into our process after many years experience specific to this industry. This broad knowledge and capability helps us to be able to scale our runs incredibly judiciously which simply helps us produce better products, faster – saving our client’s time and money.
Benefits of Custom Cable Assemblies
Fans of Livewire will know we have covered the benefits of using a custom cable assembly in our spotlight series often. Versus off the shelf options, the custom cable assembly is hands down the best solution specific to the unique issue your project faces.
Here’s our top 4 reasons you should always work with a custom cable assembly and wire harness manufacturer:
- Prototype, Prototype, Prototype
We just highlighted how prototyping is an incredibly cost effective way to ensure the production run is smooth and efficient. Prototyping helps our design team look at several different configurations simultaneously in order to source the very best components not just physically but also with the manufacturing process. Checking out the right tools from our massive tool crib, sourcing the best materials, comparing activity process times, determining the correct testing procedures to ensure product safety, integrity, and functionality – all of these processes and their associated sub processes can be tweaked to the nth degree during prototyping in order to ensure a great product that is viable to produce.
- Built-in Budget Defense
When you utilize a custom cable assembly manufacturer, you present our team with a problem and the budget we have to work with. Knowing the project parameters is the first step in the design process. Our team acts as a true fiduciary with our client’s budget. That means we treat it as if it were our own and try to get really creative in our intelligent problem solving. Any way that we can make the run more efficient means our client can allocate their budget all the more efficiently.
Off the shelf options means you are taking a chance with the product. When the application is vital, any kind of delay or malfunction costs vital time and money. Off the shelf options also don’t give you much in the way of unique configuration. Most circumstances will have at least a few attributes that are all their own. With an off the shelf option you may be left trying to make last minute corrections in order to make the component fit the situation.
- Schedule, Followed
During the design phase, our team lays out a road map for successful completion of the project with all of the necessary activities in order to get there. There are many different methods for computing project efficiency, but one industry standby and one we mentioned above is called critical path method (CPM). With CPM, all of the network activities are listed with their associated time requirements. Using a simple algorithm, you can plan your project out in order to fall under a specific time period. Completing projects on time and on budget is a skill we are proud to employ.
- Quality Assurance and Quality Control (QA/QC)
As we have highlighted, a custom cable manufacturer is only as good as its QA/QC process. Our QA/QC engineers are fantical in their approach to quality and in the continuous improvement of the process. This is one of the requirements in order to obtain and maintain ISO 9001:2015 certification. We are extremely proud to receive this designation which is an international recognition of the quality of the process, the quality of the customer experience, and the quality of the commitment towards continuous improvement. We have developed strict testing guidelines that ensures each and every product coming off our assembly line is known to be performing as it should before it ever leaves our production facilities. Our products are used in so many different vital functions – from industrial control systems, to military applications, hospitals, to global communications. Thus, our products simply must work as they are intended, cycle after cycle.
Ready to See the Benefits of a Custom Cable Assembly in Your Complex Project?
We have seen just how beneficial a trusted custom cable manufacturer can be when the situation calls for a complex solution. While the process carries a multitude of different activities in order to produce, the final product with a custom cable assembly is one that was designed and produced specific to the problem at hand.
Get in contact now to go over your specs with a knowledgeable member of the Meridian design team. You can also call us at 1-877-806-8667 or email: sales@meridiancableassemblies.com.