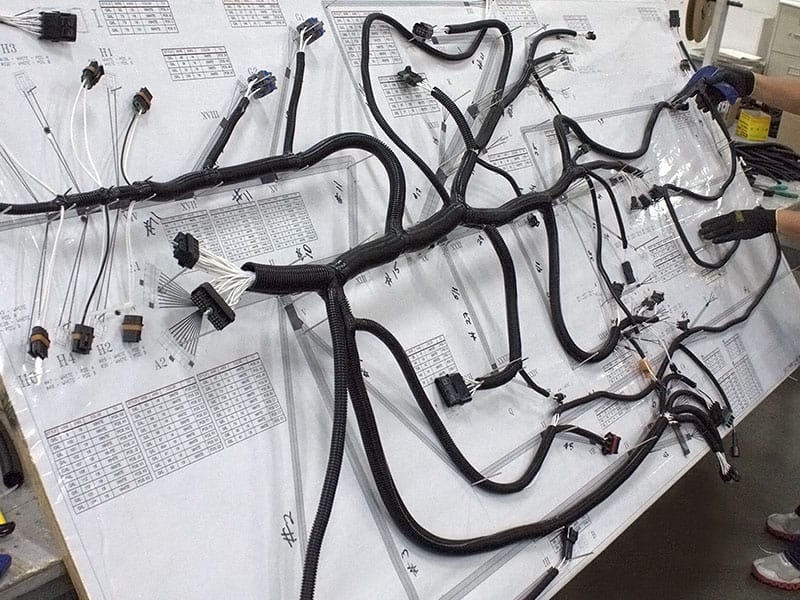
From the get go, a wire harness project can be fairly complex. Once the client has laid out their needs to our in-house engineers and designers, work begins to create the perfect solution for the unique situation. From simple hand tools through fully automated manufacturing equipment, our team employs the best techniques available in wire harness manufacturing today.
In today’s spotlight series, we’ll focus on the skills employed by our manufacturing experts and the tools they use throughout the process.
In a Land of Automation, Hand Tool Skills Still Reign Supreme
Wire harness manufacturing has never been more automated, with new technological advancements making the process so connected, so complex that you might think that the humble hand tool is simply a bygone contraption. However, even for today’s wire harness manufacturers, skills in various hand tools are necessary in order to produce even the most complex wire harnesses in use today.
Electronics infrastructure has absolutely exploded in the last decade and with it so has the need for more automated solutions. In fact, our team of expert craftsmen and women employ a bevy of sophisticated automated manufacturing and testing apparati throughout the production process. But the truth is, there are limitations to fully-automated systems that make them far more costly or time consuming than using a hand tool for a particular task.
For example, with a custom wire harness, there may not even be a tool designed yet for testing the unit to ensure its functionality, safety, and integrity. That’s when our designers in our Advanced Life Testing Lab go to work to create a custom testing unit to test the new product.
Cutting-Edge Wire Harness Tools and Products We Use Everyday
For wire harness manufacturers, the process is only as good as the tools used to produce the product and the tools are only as good as the skilled hands employing them in that process. Over decades in the industry of custom cable and wire harness manufacturing, we have built up a massive tool crib – an industry term for the tools available to complete a project – to well over 5,000 existing tools for connectors, junctions, overmolds, and housings.
These tools are used to create the cable assemblies and wire harnesses that are used heavily in the industrial manufacturing sectors, with military hardware and equipment, telecommunications, medical, and truly just about every conceivable industry out there. Our expertise with these tools allows our production team to design more than 70 percent of the assemblies and wiring harnesses Meridian produces.
While 5,000 tools would be a lot to list here, we’ve compiled some of the essential, and easily overlooked, tools and components for producing the perfect cable and wire harness for the client’s unique requirement.
- Cable tying tools – even with a fairly “simple” hand tool like a cable tie, we use a wide selection of industry-approved styles and sizes, capable of using different materials and incorporating ergonomics to aid our manufacturers in keeping consistent tension around the cables. Hand cable tying tools can either be manual or pneumatic. We can also employ fully automatic cable tying systems when high-volume manufacturing is needed.
- Cable tie mounting components – these components help to physically secure the cable ties into the rest of the assembly. With fairly broad selection here, we’re able to engineer wire harnesses with a high degree of installation flexibility.
- Fixtures for wire harnesses – another “humble” tool that can get overlooked is the uniform spacing between wire bundles, attributing for distance and height from a wire harness board. This helps create a smooth cable tie application and can be incorporated either with hand tools or an automated tooling machine.
- Printers and other media software – another easy to overlook tool in our tool crib are the custom printers and their associated software programs that allow our designers to incorporate the labels necessary to comply with set industry standards for identification and/or quality.
- Ferrules – a ferrule is a small metal or plastic ring (depending on the requirements of the application) that is crimped over a stranded wire to secure, seal, and/or reinforce the connection to a terminal. A ferrule crimping tool is a vital necessity to accomplishing this task but crimping takes far more skill than you might realize. Too much or too little pressure can have negative results for the quality of the seal.
- Built-in abrasion resistance products – our wire harness engineers have to design the perfect combination of components in order to ensure the functionality, safety, and integrity of every product we produce. Abrasion resistance products include elements like spiral wraps, heat shrinking, and grommet edging which help to protect the cables and wires, especially in tough environments.
- Terminal tools – another custom crimping tool is used to help provide the perfect crimp for terminals. Without these, the system would not be able to function as it should. We can also use a fully automated termination system to speed up the process of crimping and indexing the connectors. This helps to maintain consistent, quality terminations. In some instances, automated termination can be up to 600 percent faster than manual termination.
- Connector compression tools – there are a seemingly endless amount of compression connectors and terminals our gifted engineers incorporate into the system. Hand tools and automated compression machines help to ensure a uniform connection.
While these tools and products are undeniable necessities in our existing tool crib, we have many, many more vital tools and products at our disposal in order to produce a truly one-of-a-kind product for our clients.
Advantages of Using Automated, Semi-Automated, and Hand Tooling All in One Process
You might think that fully automated systems are the way to go and why would anyone waste time anymore with a hand tool. However, there are many applications where an automated solution simply won’t provide the efficiency we need to stick to the design schedule. Often with custom wire harnesses, we’ll have to design the tools and testing equipment needed to ensure the system works as it is intended.
Advantages to being able to employ the full spectrum of hand tools, semi-automated tooling, and fully automated tooling into our production process include:
- Maximizing Uptime: uptime isn’t a term that’s thrown around alot, instead you often hear its opposite – downtime. With that in mind, uptime is a great measure of the reliability of your system as it shows just how long our tools and machines were up, running, and/or available to be used in the process. By using a full spectrum of different levels of automation in our tooling, we can maintain a much more consistent uptime percentage, which helps keep the production process running smoothly.
- Reducing Cost: by focusing on keeping uptime percentages high, we can increase productivity which translates to lower costs.
- Staying on Budget: reducing costs helps our project managers maintain a tighter adherence to the project budget.
- Reducing Cycle Time: automation will almost always help to reduce the cycle time by increasing production speed.
- Sticking to the Project Timeline: by reducing cycle times, our project managers are able to better keep to the major project steps, which need to occur at specific timing intervals because different processes have different lead times.
- Creating Ease of Integration: as our design and manufacturing teams flex their muscle and produce custom wire harnesses that get the job done, the project would be meaningless if that component failed to integrate into the client’s electrical systems. That’s why we employ such a wide variety of tools and equipment to produce not only a functioning and safe wire harness or cable assembly, but also one that integrates easily into the client’s systems.
- Increasing Flexibility of Design Process: lastly, the diversity of tools and the requisite knowledge in using them properly means our design team has an unmatched level of flexibility for choosing the perfect amalgamation of tools and materials to get the project done on-time and on-budget.
The advantages for a custom wiring harness manufacturer having expertise and availability with hand tools, semi-automated, and fully automated tooling systems are many. While hand tooling may seem antiquated, our sophisticated operators are employing some of the most advanced tools on the planet to keep our various electrical infrastructures connected.
First Steps for Starting Your Custom Wiring Harness Project
When looking over your options for wire harnesses manufacturers out there, be sure to examine both their capability and their track record. We are both proud and humbled to have been able to produce in so many different applications. Everything from the wire harnesses used in cutting edge medical equipment saving lives, to the electrical equipment keeping our troops connected, the industrial control systems powering our nation’s largest manufacturing and municipal processes, and so many more applications over our many decades in this business.
When you’re ready to begin your custom wire harness design project, please contact our team of gifted engineers. We’ll help you create the perfect set-up for your project and have the demonstrable experience to keep the project on-time and on-budget. Contact us now to get your project started.